Polymerization
Polymerization is a chemical reaction that involves the formation of long-chain molecules known as polymers from smaller units called monomers. Polymerization reaction occurs when multiple monomers chemically bond together, forming large, complex structures. The polymerization process can be either natural or artificial. The latter process is carried out in laboratories and industries. The resulting polymers can vary widely in their properties, making them versatile materials with numerous applications across various sectors [1-4].
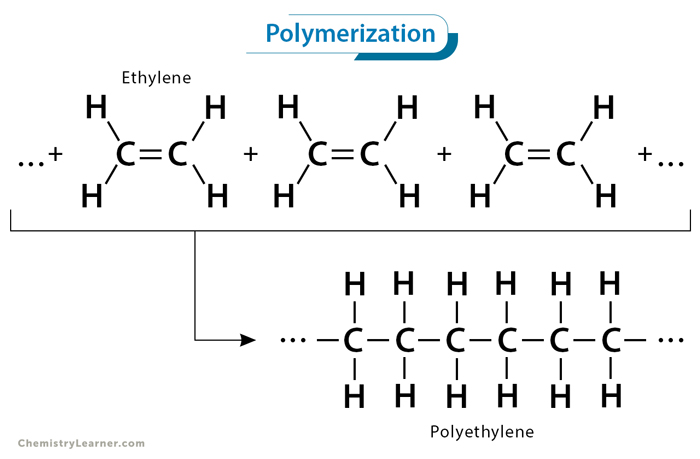
Types of Polymerization [1-8]
1. Addition (Chain) Polymerization
Addition polymerization is a chain-growth polymerization process where monomers with unsaturated double bonds react to form a polymer chain without eliminating any byproducts. In this process, the double bond of one monomer opens up, allowing it to bond with another, creating a covalent bond and extending the chain. This reaction continues until all the monomers have been consumed, forming a high molecular-weight polymer.
Examples
1. Ethylene (CH2=CH2) polymerizes to polyethylene, a versatile plastic used in packaging, bottles, and household products.
nCH2=CH2 → [-CH2-CH2-]n
2. Styrene (CH2=CHC6H5) polymerizes to polystyrene, a widely used material in manufacturing disposable cutlery, CD cases, and insulation.
nCH2=CHC6H5 → [-CH2-CHC6H5-]n
3. Propene (CH2=CH-CH3) polymerizes to polypropylene, which is used in carpeting, bottles, luggage, and exercise clothing.
nCH2=CHCH3 → [-CH2-CH(CH3)-]n
4. Vinyl chloride (CH2=CHCl) polymerizes to polyvinyl chloride, which is applied in manufacturing bags for intravenous solutions, pipes, tubing, and floor coverings.
nCH2=CHCl → [-CH2-CHCl-]n
5. Tetrafluoroethylene (CF2=CF2) polymerizes to polytetrafluoroethylene, commonly known by its trade name Teflon® and used in nonstick coating and electrical insulation.
nCF2=CF2 → [-CF2-CF2-]n

Steps
To understand the various steps involved in addition polymerization, let us take the example of the polymerization of ethylene. This reaction is carried out at high pressures in the presence of a trace of oxygen as an initiator [1].
Step 1: Initiation
The oxygen in the reaction reacts with ethene to give a peroxide, which is very unstable. The peroxide decomposes into free radicals upon reacting with light or heat. These free radicals are the chain carriers.
R-O-O-R → 2 R-O·
Step 2: Propagation
The free radical from the first steps adds to the ethene, breaks the pi-bond, and bonds firmly with one of the carbons. The remaining electron from the pi-bond is used to form a new free radical. The new product adds an ethene molecule in a chain reaction.
R-O· + CH2=CH2 → R-O-CH2-CH2·
R-O-CH2-CH2· + CH2=CH2 → R-O-CH2-CH2-CH2-CH2·
Step: Termination
The chain is terminated when two free radicals combine, and none is left to initiate another reaction.
R-O(-CH2-CH2-)n· + ·(-CH2-CH2-)mO-R → R-O(-CH2-CH2-)n+m-O-R
2. Condensation (Step-growth) Polymerization
Condensation polymerization is a step-growth polymerization process involving the reaction between two monomers, forming a polymer and a small molecule as a byproduct. Unlike addition polymerization, condensation polymerization typically involves monomers with two different functional groups. The reaction occurs by eliminating small molecules, such as water, alcohol, or ammonia, as the polymer chain grows. Condensation polymerization is crucial in producing synthetic fibers, fabrics, and plastics with specific properties, making it an essential process in the textile and polymer industries.
Examples
1. Formation of nylon-6,6 involves adipic acid reacting with hexamethylenediamine and producing nylon polymer and water as a byproduct.
2. During the synthesis of polyester, diol and dicarboxylic acid combine to form the polymer while releasing water molecules.
Condensation polymers generally form more slowly than addition polymers and typically require heat. Additionally, they possess lower molecular weights. During the late stages of polymerization, the terminal functional groups in condensation polymers remain reactive, merging shorter chains into longer ones. The existence of polar functional groups on the chains can significantly enhance chain-chain interactions, mainly when hydrogen bonding occurs. This phenomenon boosts crystallinity and tensile strength.
Classification of Polymers Based on Structure
Polymers can be classified based on their structure into three main categories: linear, branched, and crosslinked polymers. These classifications depend on the arrangement of polymer chains and the degree of connectivity between them. [6]
Linear Polymers
Linear polymers are characterized by long, unbranched chains of repeating monomer units. The monomers are successively linked, forming a straight chain without substantial branching points. Due to their simple and well-defined structure, linear polymers exhibit excellent processability and are relatively easy to synthesize. They typically possess high flexibility and can align closely with one another, leading to enhanced mechanical properties. Common examples of linear polymers include high-density polyethylene (HDPE), polyvinyl chloride (PVC), and polypropylene (PP).
Branched Polymers
Branched polymers have side chains or branches stemming from the main polymer backbone. These branches can emerge at various points along the chain, creating a more complex and interconnected structure. The presence of branches reduces chain mobility, affecting crystallinity and density. They influence the material’s mechanical properties, such as its elasticity and toughness. Some well-known branched polymers include low-density polyethylene (LDPE) and highly branched dendritic polymers.
Crosslinked Polymers
Crosslinked polymers, known as network polymers, feature covalent bonds between different polymer chains. These crosslinks create a three-dimensional network, creating a rigid and insoluble material. Crosslinking can occur during the polymerization process or through post-polymerization reactions. This unique structure imparts exceptional strength, thermal stability, and resistance to solvents and chemicals to crosslinked polymers. They often find application in producing rubbers, coatings, adhesives, and thermosetting plastics. Examples of crosslinked polymers include vulcanized rubber, epoxy resins, and polyurethanes.
Great explanation